10年磨一剑,从“跟跑”到 “并跑”,致力于解决我国在水下油气开采控制领域的卡脖子技术,哈工程机电学院水下作业技术与装备研究所王立权教授团队,研发的水下油气开采“最强大脑”水下生产系统核心控制装备近日完成交付,将应用于渤海油气田开发项目。
该装备是国内首台套应用于渤海油气田开发的国产水下控制系统,各项指标达到国际同等水平,并通过挪威船级社(DNV)认证。项目甲方中海油研究总院认为,这标志着我国高端海洋油气关键装备国产化取得重要突破,开辟了浅水油田作业新模式。
打破垄断技术,向世界证明中国行!
渤海石油矿藏丰富,但水上航道纵横,无法采取传统的海上平台的直采方式,而使用水下生产系统实现海底油气开采并将油气输送到远距离海洋平台是最佳途径。在复杂的海底环境中,如何安全可靠地实现对油气开采装备的控制是核心关键,这项核心技术业内被称为水下控制模块(SCM)。
水下控制系统的相关技术和装备,仅被欧美少数几家公司垄断。因水下作业对设备安全性和可靠性标准要求极高,一旦发生泄漏问题,将对海洋生态造成严重损害。面对这项高风险和高技术研究,国内高校和研究单位极少涉及。甚至国内外业界也有人认为“这么高端的设备中国短时间造不出来”。
学校水下作业技术与装备研究所潜心钻研,在渤海浅水油田开发项目中,用三年的时间,攻克了水下控制系统的主要核心技术和装备制造技术——水下控制模块(SCM),向世界证明了“我们可以”。
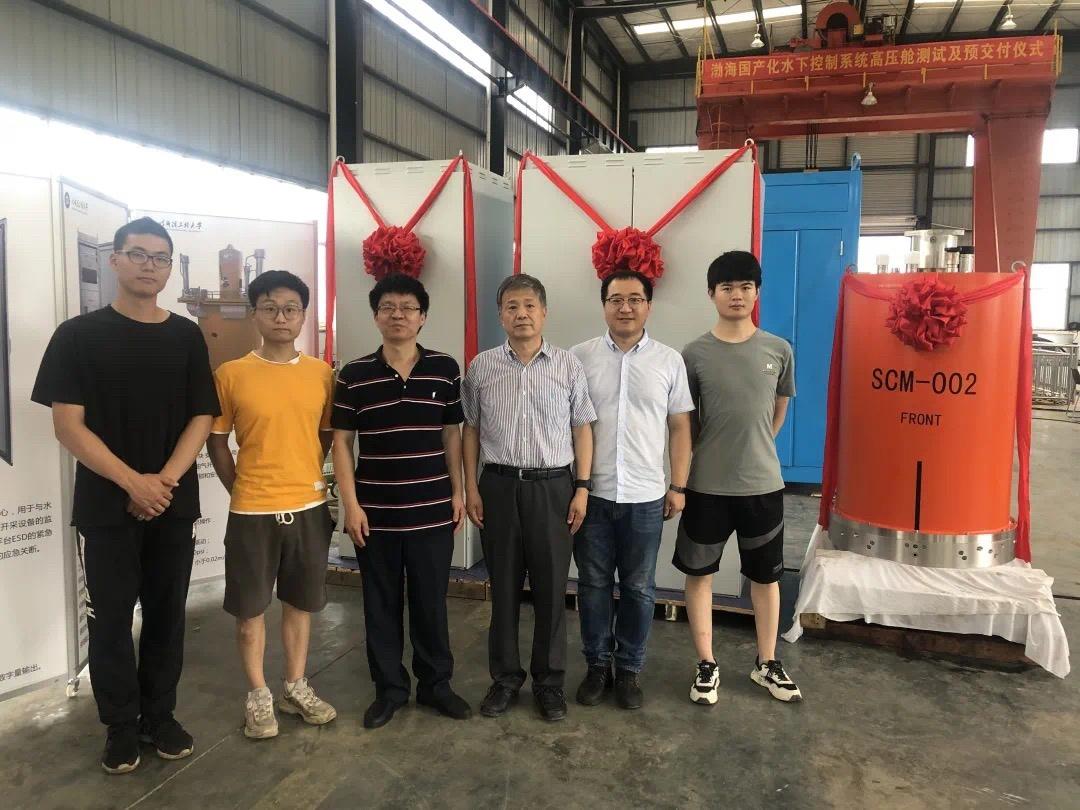
水下控制系统研发团队合照
水下控制模块(SCM)作为水下控制系统的“大脑”,是一个机、电、液、光一体化的设备,从设备细节到整体系统都要经受高温、高压、高强度冲击振动的考验,需解决多学科难题。
液压上要求所有液压元器件特别是液压集成阀板承受10000psi的高压,不允许有一丝一毫的渗漏。经受住如此高压,才能满足设备水下作业需求条件。“这些直径8mm液压接头,要承受700多公斤的重压,相当于两个世界举重冠军的举重成绩。”研发人员贾鹏说。电气上要求全冗余化控制,控制系统要能承受70度高温环境。机械上要解决14路液压接头和4路多芯电接头同步精确对接和锁紧问题。这些难题均被团队一一攻克。
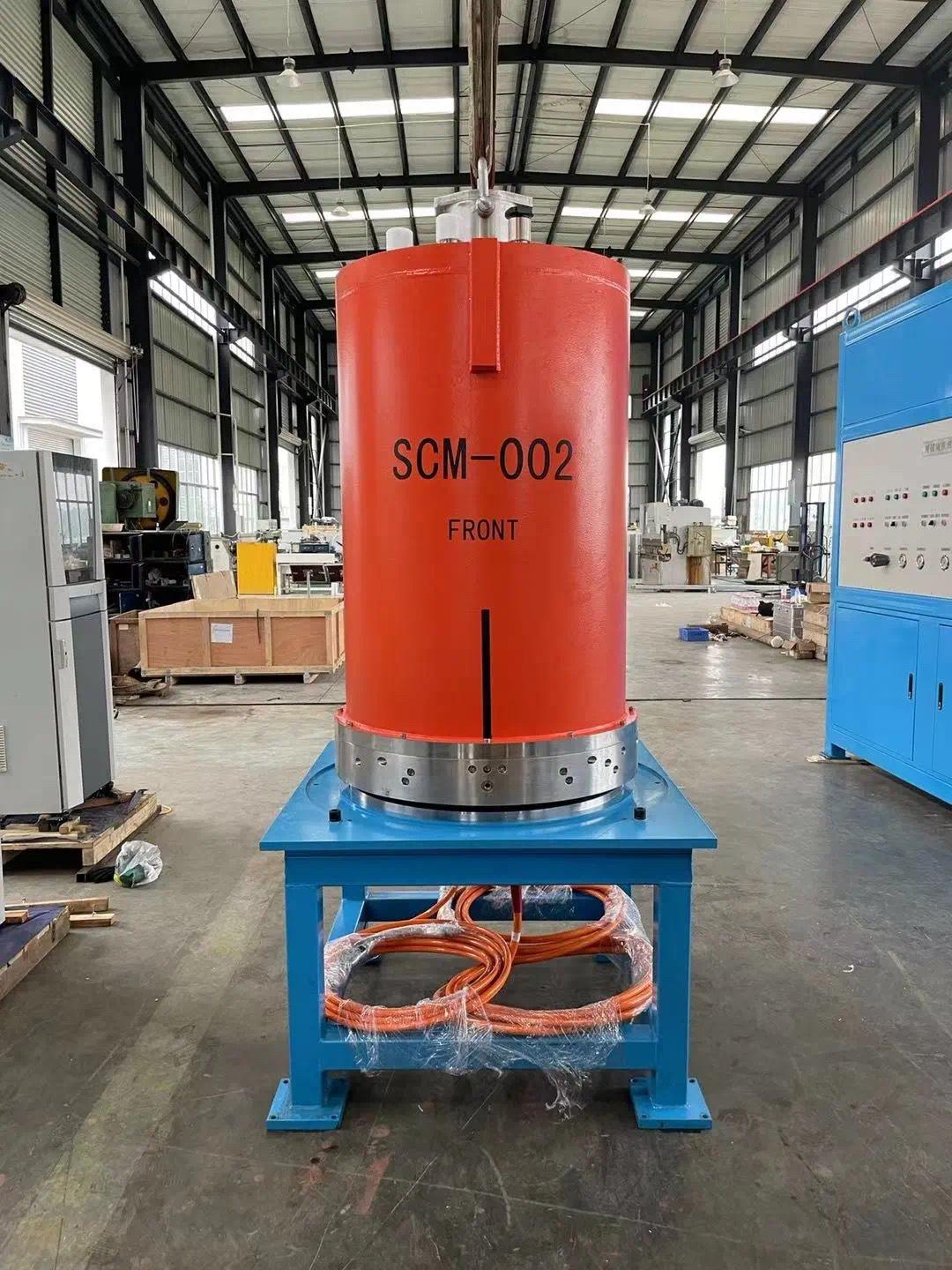
水下控制模块
除解决水下控制模块(SCM)的技术难题,渤海海生物生长快,泥沙含量大、海水浑浊和温差大的现实问题,同样为项目研发带来诸多挑战。为了防范海生物对设备的影响,课题组专门研究了渤海环境海生物的生长规律,并针对性地通过材料、涂层和防护结构防止海生物对设备的影响;渤海环境泥沙含量大、海水浑浊,能见度低,给潜水员水下操作带来很大困难,课题组和一线潜水员沟通,从设备操作标识、操作灵活性等方面优化了操作接口;渤海环境温差大,对系统的硅油补偿提出了更高的要求,项目组通过选择特种硅油,扩大补偿囊体积和减少补偿空间等方法解决了温差大造成的补偿难题。
逢山开路、遇水搭桥,水下作业技术与装备研究所团队突破水下高压集成式液压阀板、水下多路液压电气回路自动精确对接、锁紧解锁、SCM安装及回收、双SEM冗余控制、水下供电单元电力智能监控和主控站多路数据处理等多项核心技术,成功研制了具有自主知识产权的水下控制模块(SCM)、主控站、电力单元和安装回收装备。为水下油气开采成功研制出“最强大脑”。
十年磨一剑,从跟跑到并跑
渤海油气田项目水下控制系统装备成功问世源自科研团队 “咬定青山不放松”的十年积累。团队自2011年就瞄准高端海洋油气关键装备研发,他们潜心研究核心技术和装备制造工艺,从“跟跑”做到了与国际 “并跑”。
“核心技术要努力掌握在我们自己手里。” 2011年团队以测试方身份参与进入国家某重大项目,要通过水下控制模块(SCM)对整个水下控制系统进行全方位测试,直到任务开展,团队才发现,作为核心技术,控制模块SCM的结构尺寸、接口关系、通信协议等标准均被国外封锁。团队迎难而上,顶住压力,成功研制出了水下控制模块的原理样机,顺利完成了整个水下系统的测试任务。
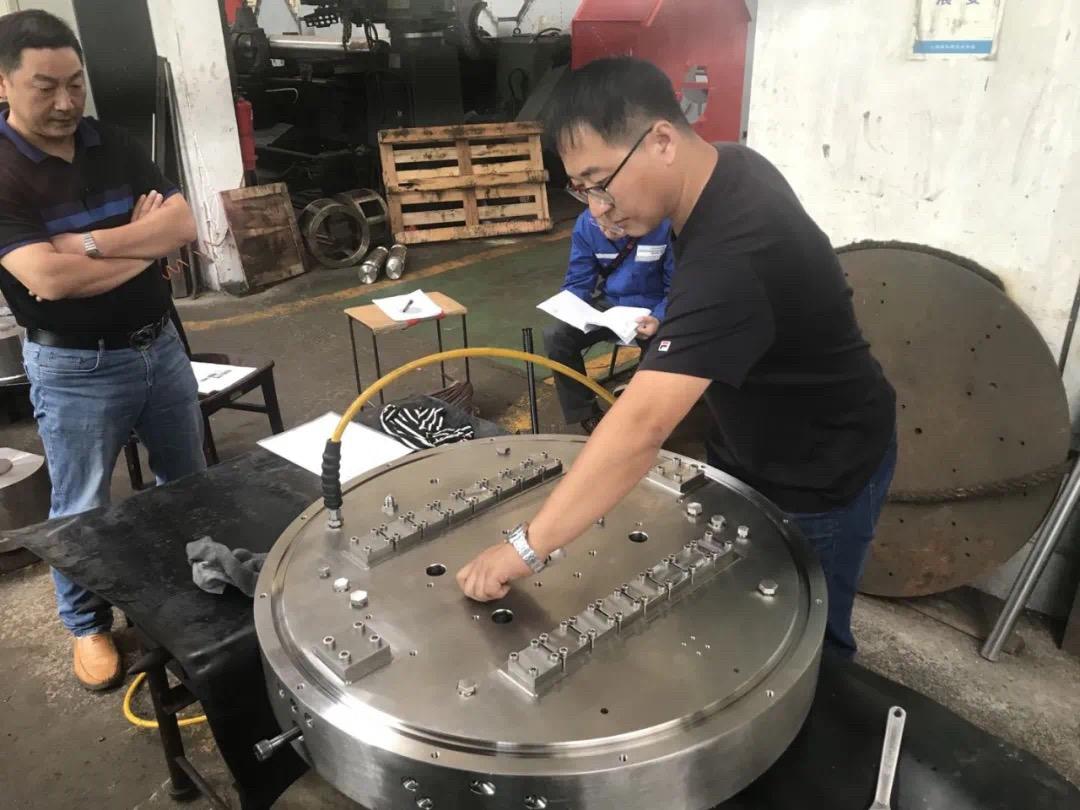
水下控制系统的组装与现场测试
“虽然遇到很多难题,但我们也找到了自信,终有一天技术一定会掌握在我们自己手里”,团队负责人王立权说。
2013年,团队参与到国家863重大研究项目,这是团队对水下生产系统控制理解的一次全面深化。团队要完成水下控制模块的分离对接,直径1米,高1.8米、重达3吨的水下控制模块要实现与其他装备的完美对接、分离,涉及十几路电、液回路同时对接、分离,是机械里的尖端技术。
“为了攻克尖端难题,我们一宿一宿地泡在实验室,大家很有精神头,全身心投入”,也正是在这次任务中,团队完成了SCM工程试验样机研发,全体人员加深了对水下生产系统控制的认识。

水下控制模块顺利完成对接试验
2015年,团队参与水下控制系统关键器件和对中锁紧机构攻关,涉及构型设计、理论分析、材料研发实验验证等诸多环节,通过研发,团队顺利完成系统可靠性提高、尺寸缩小的目标,“完成任务的那天,我们给自己放了一天假,第二天全体就再次回到岗位上”,这次科研攻关,团队全面深入掌握了实际应用装备研发制造的核心技术。
从水下控制模块的原理样机、工程试验样机、工程样机到实际应用装备,水下作业技术与装备研究团队一步一个脚印,不断磨练真本领,练就了敢接重大任务的底气,竖起了敢打敢拼、敢于攻克技术难题的旗帜。2019年,团队果敢挑起渤海油气田项目水下控制系统装备研发重任,历经三年,再次交上一份完美答卷。
10年的执着、拼搏和成长,他们成为国内高校唯一一所研制出水下油气开采的“最强大脑”,填补国内技术空白、攻克水下控制卡脖子技术的团队。
为国担当的使命,练就“科研狂人”
“您都60多岁了,马上要退休了,干嘛还这么拼?”“因为团队在这个领域有十几年的技术积累,不只是我,团队每个成员都憋着一股劲,要为国家设计制造出第一套水下生产系统控制装备,并获得首次应用,为能实现这个目标感到自豪”,团队负责人王立权这样回答身边人的提问。
团队4名教师,10多名博士学生,却数十年如一日,把严谨、创新、求实的工作作风和敢拼必成的信念投入到无数个科研日夜中,用硬实力赢得了业界尊重,也赢得了国内外同行的赞扬。
7月份正是炎热时节,在成都高压舱试验,工期非常紧张,四位团队老师和多名同学在试验场地连续奋战两天两夜,顺利完成水下生产系统控制装备的高压舱试验。

水下控制系统成功完成高压舱测试
当时王立权虽身体不适,面色发白,依旧坚持在现场,直到试验顺利完成。
作为试验评价方,素以考评严格著称挪威船级社DNV人员深受感动,一大早为四位老师购买了早餐,并且赞道:“哈尔滨工程大学的老师亲力亲为,是学习的榜样。”

水下控制系统交付甲方
团队成员不仅是攻关科研一线的技术难题的尖刀,同时也是生产一线的质量把关员。水下控制模块的机械加工装配在齐齐哈尔第二机床厂完成,但因水下控制模块属于特种设备,水下控制模块涉及到水下14路液压接头和4路多芯电接头同步精确对接,加工时对焊接工艺、振动时效处理、加工尺寸形位公差和装配工艺要求非常高。放心不下的贾鹏奔赴现场,两个多月的时间里,和二机床的工人师傅们摸爬滚打在一起,对于水下控制模块的每条焊缝质量,每道加工装配工艺,每个公差尺寸进行严格把控,直到水下控制模块对接试验成功。
为制造第一套国产水下生产系统控制装备而拼搏,这份融入骨血的使命担当,让团队成员克服万难。“科研在外,爱人怀孕,王向宇默默把妻子送回家请父母照顾”“疫情期间,贾鹏出差三个月未回家,女儿就常问妈妈,爸爸去哪了?我想他!”“早上5点出门,夜里11点回家,团队成员每天都要去20公里外的工厂,春节也不例外”“团队硕博研究生陶浩涵、商守博等学生,放弃寒暑假休息,每晚与老师熬至深夜完成科研任务”……
这些“科研狂人”攻克一个个技术难关,冶炼炽热的使命情怀。做 “顶天立地”的真科研,把科研书写在祖国大地上,这是他们为什么能,为什么行,为什么始终向一流进军的信念支撑。
原文链接:http://h5.hljnews.cn/h5/detail/normal/4377028689871872